
Li-ion Battery Recycling Plant Feasibility Study
SCM excels in providing comprehensive turnkey solution (PMC) for lithium-ion battery recycling, ensuring efficient processes from beginning to end. Equip your business with critical insights and detailed analysis before making your strategic decisions.
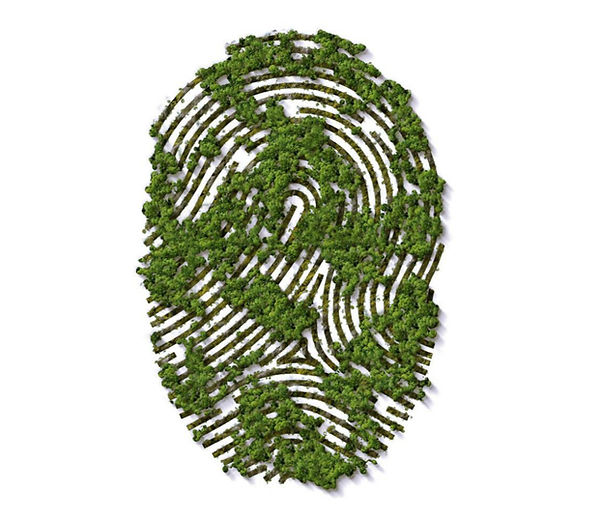
Feasibility Study: Establishing a Lithium-Ion Battery Recycling Plant
With the electric vehicle market continuing to grow, the demand for lithium-ion batteries is on the rise. This study examines the feasibility of setting up a lithium-ion battery recycling plant in India, focusing on addressing environmental challenges and taking advantage of the booming e-mobility sector.
Battery Chemistry & Design:
-
Detailed Breakdown: Understand the structure of lithium-ion batteries, including the roles of the anode, cathode, electrolyte, and more.
-
Design Features: Explore key design elements like separators, current collectors, casing, temperature regulation, and voltage control that contribute to battery performance and safety.
-
Advanced Chemistries: Learn about different battery types—such as Lithium Iron Phosphate (LFP), Nickel Manganese Cobalt (NMC), and emerging solid-state technologies—each with unique strengths and applications.
Composition & Materials:
-
Component Analysis: Delve into the materials used in lithium-ion batteries, from graphite and lithium salts to copper and aluminum collectors. Learn how the composition impacts energy storage, cost, and safety.
-
Emerging Trends: Discover innovations in cathode materials that offer improvements in energy density, safety, and longevity, especially for applications in EVs and renewable energy.
The Growing Need for Recycling:
-
Resource Conservation: Understand the critical role of recycling in conserving essential materials like lithium, cobalt, and nickel, reducing dependence on mining and lowering environmental impact.
-
Environmental Protection: Learn how proper recycling prevents hazardous waste, reduces carbon emissions, and complies with global environmental regulations.
-
Energy Conservation: See how recycling minimizes energy consumption, from mining and refining to transportation and manufacturing, while reducing carbon footprints.
Why India Needs Recycling:
-
India’s Green Push: With EV adoption and renewable energy storage on the rise, India is experiencing unprecedented demand for lithium-ion batteries. Our study explores how recycling can meet this demand sustainably.
-
Government Initiatives: Discover how initiatives like FAME and NEMMP are driving the market for EVs and lithium-ion batteries, making recycling an essential industry.
A Sustainable Future:
This report outlines how recycling lithium-ion batteries can conserve resources, protect the environment, and lower energy consumption, helping you navigate the complex but essential landscape of battery recycling.
What You’ll Get:
-
Comprehensive analysis of lithium-ion battery chemistry, design, and components.
-
The latest trends in battery technology and market demands.
-
Strategic insights into the benefits of recycling for resource conservation and environmental protection.
-
Actionable data for developing sustainable recycling practices in India and beyond.
LIBs Market Outlook:
-
A thorough analysis of the EV boom driving demand for lithium-ion batteries (LIBs).
-
Forecasts showing the explosive growth of EV sales from 10.5 million in 2022 to 27 million by 2026.
-
Insights into solid-state batteries, next-gen chemistry, and sodium-ion tech reaching commercialization.
-
Key data on global EV adoption rates by region—52% in China, 42% in Europe by 2026.
Battery Recycling Market Insights:
-
Market projections of US$5 billion in 2022 growing to US$23.6 billion by 2030 at a 21.4% CAGR.
-
A deep dive into regional developments, particularly in China, Europe, and the US, where end-of-life battery volumes are expected to surpass scrap production by 2030.
-
India’s growing market, with an anticipated $1 billion recycling opportunity by 2024, as the country’s recycling capacity scales up to meet the rising demand.
Key Industry Players and Global Capacity:
-
A comparison of leading global and Indian battery recyclers, showcasing their capacities and technologies.
-
Detailed breakdown of recycling methodologies, from mechanical to hydrometallurgical processes, tailored to the Indian market.
-
Profiles of top recyclers like Lohum, Attero (India), and their global expansion plans.
Strategic Opportunities:
-
Insights into government policies, subsidies, and regulations driving the localization of battery supply chains.
-
An exploration of the environmental benefits of recycled battery materials, which produce 4x lower carbon emissions compared to virgin materials.
Technical Feasibility:
Technology Solutions
-
Pre-treatment: Introduction to necessary pre-treatment methods, such as mechanical separation and thermal treatment, to prepare batteries for recycling.
-
Direct Recycling Method: Focus on preserving the cathode’s crystal structure to make recovered materials reusable with minimal treatment. This section includes steps like battery collection, sorting, shredding, and electrolyte recovery.
-
Pyrometallurgy: A high-temperature process used to separate metals from battery waste. It discusses techniques like smelting, calcination, and roasting to recover valuable materials such as cobalt, nickel, and copper from batteries.
-
Hydrometallurgy: A low-energy, highly efficient recycling process that uses chemical leaching to extract metals from the battery waste, minimizing environmental impact.
Site Feasibility
-
Location Assessment: Criteria for selecting the best plant site, including industrial zoning, access to utilities (power, water, etc.), transportation networks, and proximity to battery supply sources.
-
Utility Assessment: Detailed evaluation of the energy, water, and waste disposal requirements for operating a recycling plant, ensuring minimal environmental impact.
Process Flow
-
Proposed Phase Plan: A phased approach to plant setup, from initial construction and equipment installation to full operational capacity. Each phase is designed to optimize resource use and efficiency.
-
Process Flowchart: A visual representation of the recycling process, from battery collection and pre-treatment to final material recovery, offering a clear understanding of how the plant will operate.
Financial Feasibility:
Cost of Project
-
Detailed breakdown of the initial capital investment required for setting up the plant.
-
No. of scenarios are considered.
-
This section includes a comparison of costs for land acquisition, construction, machinery procurement, and initial operational setup.
Raw Material Cost
-
Year 1 to Year 5 projections for the costs associated with acquiring used lithium-ion batteries and other necessary raw materials.
-
Assessment of market volatility and expected fluctuations in material prices over the plant’s operational period.
Revenue Projections
-
Estimated revenue generation based on recovered materials like lithium, cobalt, nickel, and copper.
-
Separate revenue models for different country setups, factoring in machinery efficiency and product quality.
-
Revenue estimates for the first five years, including potential fluctuations based on market demand for recycled battery materials.
Profit and Loss Analysis
-
Profit and loss scenarios over the first five years of operation.
-
Projections based on different machinery setups, market prices, and operational costs.
-
Break-even analysis indicating how long it will take to recover the initial investment.
-
Risk factors such as raw material cost fluctuations and market demand changes are considered.
Regulatory & Legal Compliance:
Policies
-
Overview of critical battery and waste management regulations:
-
Battery Management and Handling Rules (BMHR) 2001
-
E-Waste (Management) Rules 2016
-
Battery Waste Management Rules 2022
-
-
Amendments and updates to these policies and their impact on battery recycling operations.
Required Permits and Licenses
-
A comprehensive list of the permits and licenses needed to set up and operate a battery recycling plant:
-
Land allotment approvals
-
Pollution-related certifications (e.g., air and water quality permits)
-
Business setup licenses
-
Other necessary environmental clearances and operational permits.
-
Risk Screening and SWOT Analysis:
Risk Across the Value Chain
-
Analysis of risks at different stages, including:
-
Collection and transportation of batteries
-
Storage and handling risks related to safety and hazardous materials
-
Recycling operations risks (e.g., environmental pollution, air quality issues, waste disposal)
-
SWOT Analysis
-
Strengths: Growing demand for recycled materials, strong market potential.
-
Weaknesses: High initial costs, regulatory challenges, and technical complexity.
-
Opportunities: Expanding EV market, global push for sustainability, growing need for critical materials.
-
Threats: Fluctuations in raw material prices, evolving regulations, competition from established players.
Supply Chain Dynamics of LIB Recycling Plant:
Proposed Phase Plan for the Project
-
A phased approach for the project setup, outlining timelines for:
-
Initial procurement
-
Construction
-
Commissioning
-
Full-scale operation
-
List of Contacted LIB Recycling Machinery Manufacturers
-
Detailed list of local and global manufacturers of LIB recycling machinery.
Raw Material Suppliers
-
Local and International Market Scrap Suppliers: Identifies suppliers for sourcing used batteries for recycling.
-
List of OEMs for Collaboration on EPR: Companies to collaborate with for Extended Producer Responsibility (EPR).
List of Potential Black Mass Buyers
-
Identifies the potential buyers for black mass (a critical output of battery recycling).
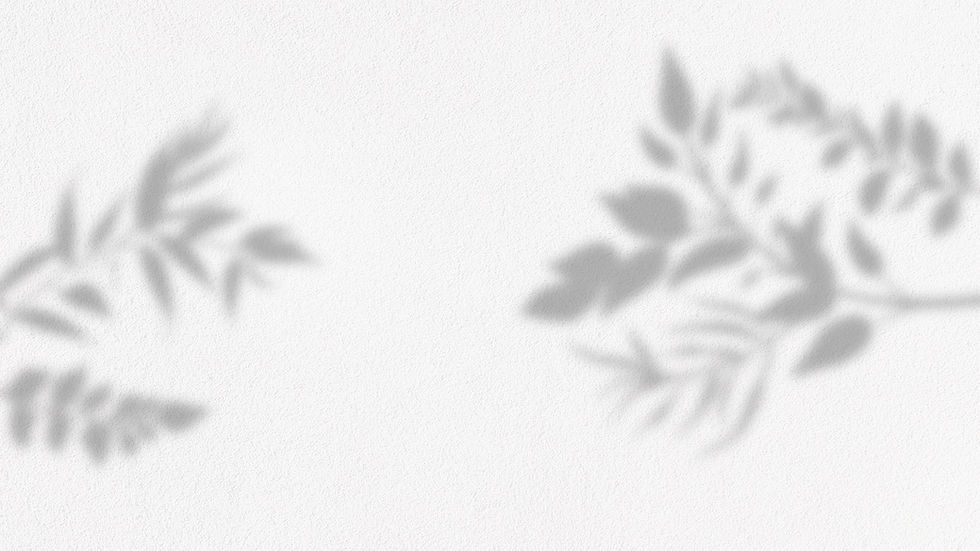